Ensuring pristine water quality is paramount in any aquatic facility, meeting the dual objectives of customer satisfaction and regulatory compliance. Central to this process are pool filter systems, integral components within a pool’s cleaning regime, alongside recirculation and disinfection systems.
But how do pool filter systems work? In essence, the filtration mechanism captures water circulated by pumps. The water moves over the filter, where impurities are caught within a layer of sand, glass, or alternative materials known as filter media. This process ensures that the water is free from undesirable particles and returns to the swimming pool fresh and clear.
In today’s landscape, cutting-edge pool filter systems transcend mere cleanliness. They redefine efficiency, ushering in an era of sustainability and cost savings, setting new benchmarks in the aquatic facility field.
Dive deeper with the eBook


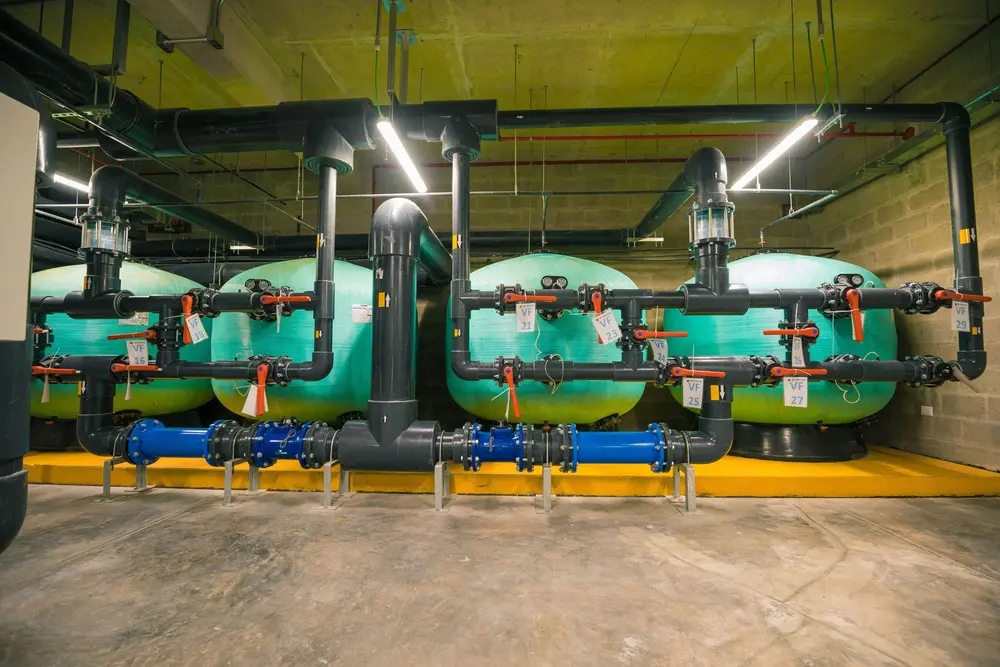
Types of pool filter systems
There are various types of pool filter systems on the market, each with their distinctive features, advantages, and applications. Their differentiation lies in the materials employed during manufacturing, their finishing, and the type of filter media they utilize.
Materials for tank and external housing construction
- Steel (carbon-reinforced or stainless): Although rarely utilized in modern systems, this option is characterized by its high cost. Although in some markets it’s still a common option.
- Thermoplastic: Optimal for smaller residential pools, thermoplastic pool filter systems offer versatility with options such as injection-moulded plastic, blow-moulded, and roto-moulded variations.
- Glass-fiber reinforced plastic (GRP): Predominantly chosen for commercial pools, GRP has become the material of choice due to its robust chemical and mechanical resistance, ensuring an extended service life.
Filter finishes
- Bobbin-wound: Crafted from glass-fiber reinforced plastic, this type of filter finish boasts complete anti-corrosiveness, coupled with high mechanical, chemical, and thermal resistance. Particularly resistant to corrosion, fiberglass filters are the preferred choice for pretreating salt or saline water processes. Comprising an interior barrier coating of isophthalic resin and a bobbin-wound exterior with GRP (following standard UNE-EN 13121), these filters can be designed with a cylindrical shape, a collector system, and connections tailored to specific requirements.
- Laminated: This variant is manufactured through the simultaneous spray-up of resin and fiberglass, providing a resilient finish.
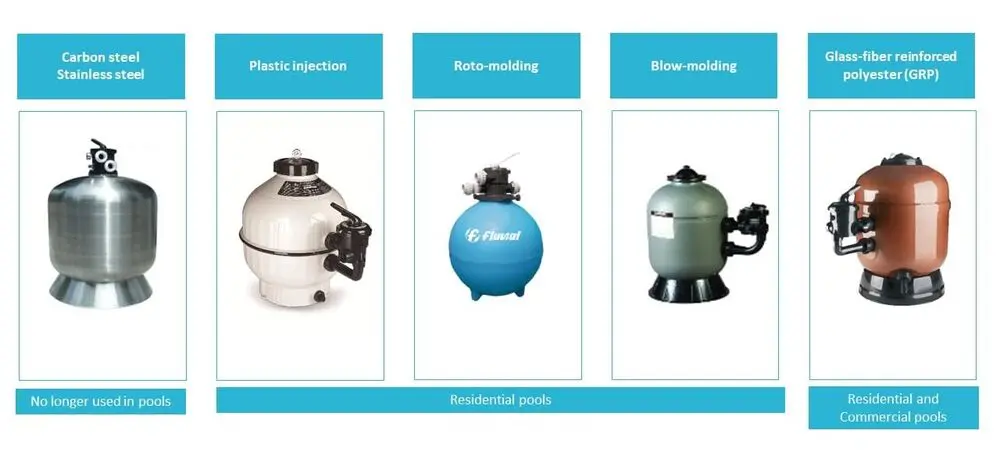
Selecting the right filter media
In pool filter systems, the heart of the operation is the filter media. Filter media is a granulated material placed in the filter, where water sheds its impurities and debris. Choosing the right filter media involves considering a few key factors.
The height of the filter bed is crucial, which will be determined by the filter media chosen. Public pools typically go for filter beds ranging from 900 to 1,200 mm, allowing for various filter bed types and versatile multilayer setups. Residential pools, on the other hand, usually make do with a more modest range, falling between 300 and 800 mm.
Granulometry, or the size of the granules in the filter media, is of greater importance. Smaller granules are good at trapping tiny dirt particles but tend to clog up faster. The common granule size is between 0.4 and 0.8 mm, maybe 1-2 mm per layer if it’s made of gravel.
Durability is also key. Regularly checking the filter’s condition ensures the bed depth is good and it expands as expected during backwashing. If not, it’s time for a replacement.
There’s a variety of filter media out there, including
- Anthracite and silica sand: Silica sand is the most common and can be used as the only filter medium. Nevertheless, in commercial filters pool filters are usually combined in a multilayer. This combination uses anthracite placed on top of silica sand. With a minimum height of 600 mm and gravel at the base, it effectively catches larger particles. This split reduces the buildup of impurities in the initial stretch of sand, extending the time between backwashes and saving water.
- Glass: Known for its even distribution of trapped dirt across the whole filter bed, glass filter media minimizes clogging in the initial stretch, leading to longer intervals between backwashes. Plus, it reduces working pressure compared to silica sand.
- Zeolite: A naturally porous material, zeolite beats sand in filtration efficiency. It’s durable and reasonably priced.
- Perlite: Doing wonders in modern regenerative filters, perlite comes from volcanic rock. Heated up, perlite expands to 20 times its original volume, becoming an excellent filter media.
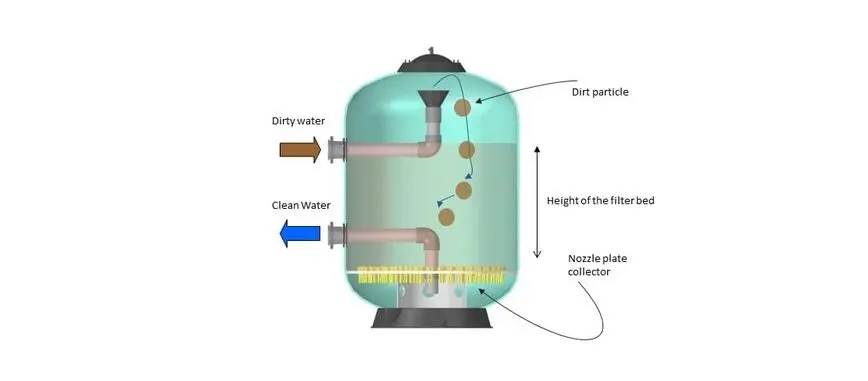
Rational use of resources through pool filter systems
Maintaining hygienic and aesthetically pleasing pool water requires the use of pool disinfection products, whether they be chemicals like chlorine or innovative salt electrolysis systems.
To reduce spend on chemicals and prolong the lifespan of disinfection systems, emphasis should be placed on filtration, otherwise known as physical treatment. This approach allows chemical treatments to be reserved for addressing issues not effectively resolved through filtration.
Let’s look at the essential maintenance practices.
Backwashing
Periodically reversing water currents, backwashing serves to dislodge and expel any trapped dirt particles within the filter media. This routine is recommended every two weeks, or at least once a month, depending on factors such as pool size, usage patterns, and the characteristics of your filtration system.
The frequency of backwashing hinges on the filter head loss, calculated by subtracting the highest pressure reading from the lowest displayed on the gauges. If the result exceeds 0.6 bar, initiating a backwash is advisable. A prudent approach involves more frequent, shorter backwashing sessions, reducing power consumption and maintaining a stable filtration flow rate.
Air scouring
To increase the efficiency and sustainability of the backwashing process, this can be combined with air backwashing in the first stage, thus reducing water consumption. The air scouring process injects air through a dedicated connection at the filter’s base or via the backwash water inlet. Notably, air scouring consumes only electricity, enhancing its efficiency compared to conventional backwashing methods.
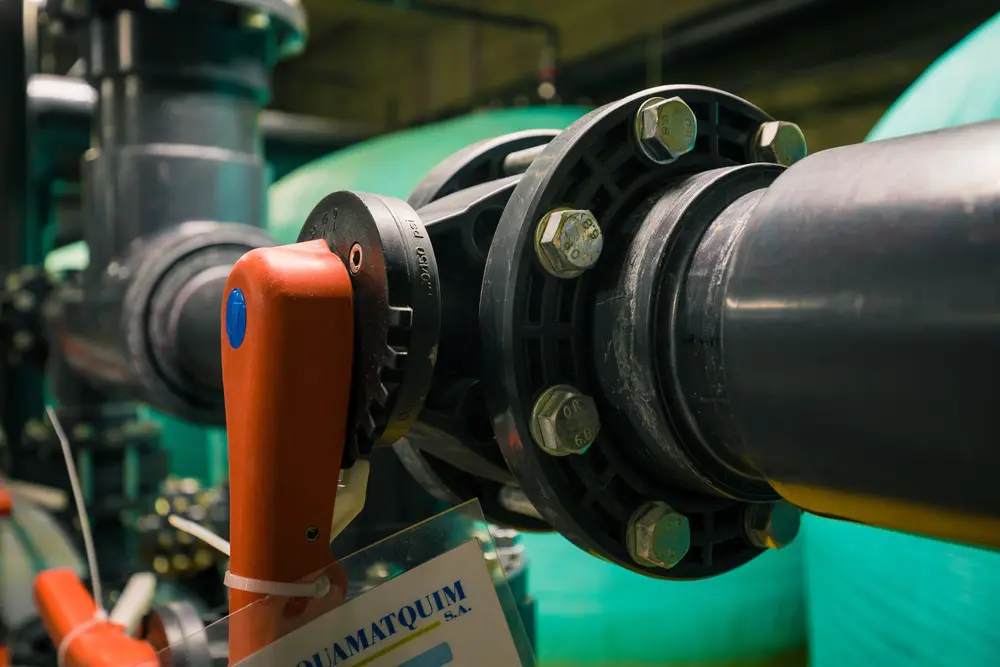
Regenerative filters
Nowadays, a noteworthy technology has emerged in the realm of pool filtration – the regenerative filter. Praised for its exceptional efficiency and sustainability, this innovative system utilizes regenerative filter media to effectively trap dirt particles.
The distinguishing feature of regenerative filters lies in their utilization of flexible tubes coated with perlite. These tubes capture particles on their surface, and when the perlite reaches saturation, the filter undergoes a remarkable self-regeneration process through vibration.
This unique mechanism not only ensures efficient filtration but also contributes to significant energy savings, with these pool filter systems capable of reducing energy consumption. Additionally, they play a crucial role in minimizing chemical usage, delivering substantial savings.
The advent of regenerative filters represents a transformative shift in pool filtration technology, offering a pioneering solution for those seeking efficient and sustainable pool maintenance practices.
Choose the right system for pristine waters
Pool filter systems are the linchpin for maintaining impeccable water quality. Operating seamlessly alongside recirculation and disinfection systems, these filters undergo an intricate process, ensuring the elimination of pathogens and unhygienic particles before the treated water returns to the pool.
In today’s landscape, modern pool filter systems extend beyond mere cleanliness, offering efficiency that redefines sustainability and cost-effectiveness. With diverse types catering to specific needs, emphasis on filter media selection plays a pivotal role.
While advancements like regenerative filters offer notable benefits, the entire spectrum of pool filter systems represents a transformative shift in technology, providing a pioneering solution for those committed to efficient and sustainable aquatic facility management. For the forward-thinking professional, exploring this spectrum is a pathway to elevated standards in pool maintenance.